Tecnologías para sistemas de mezcla industrial
VMI lleva más de 70 años desarrollando tecnologías innovadoras para optimizar la fabricación de productos líquidos y semisólidos en los sectores de la cosmética, la farmacia y la química de especialidades. La experiencia de nuestras oficinas de ingeniería permite desplegar instalaciones de mezcla eficientes y personalizadas según sus necesidades.
Automatización
Los sistemas de control desarrollados por VMI están diseñados para responder a las normas y reglamentos de las industrias farmacéutica y cosméticas (GAMP5, 21 CFR parte 11, S88). Integramos los Sistemas de Supervisión, Control y Adquisición de Datos de referencia, como Siemens, Wonderware o Rockwell. Nuestras interfaces de operario son completas e intuitivas, con módulos dedicados a las necesidades específicas de sus procesos. Nuestras IHM permiten:
- El control del funcionamiento y de los parámetros de una línea completa de producción
- La programación de recetas
- La visualización y el análisis de datos. Estos informes permiten analizar la gestión de los procesos de fabricación e identificar las áreas de optimización: ajuste de parámetros, consumos, mantenimiento del equipo y de sus componentes, etc.
- La trazabilidad de los lotes
- La reproducibilidad de los procedimientos de producción y de limpieza.
- La durabilidad del equipo gracias a las soluciones de metrología y de mantenimiento
Dosificación, transferencia y almacenamiento de las materias primas y los productos acabados
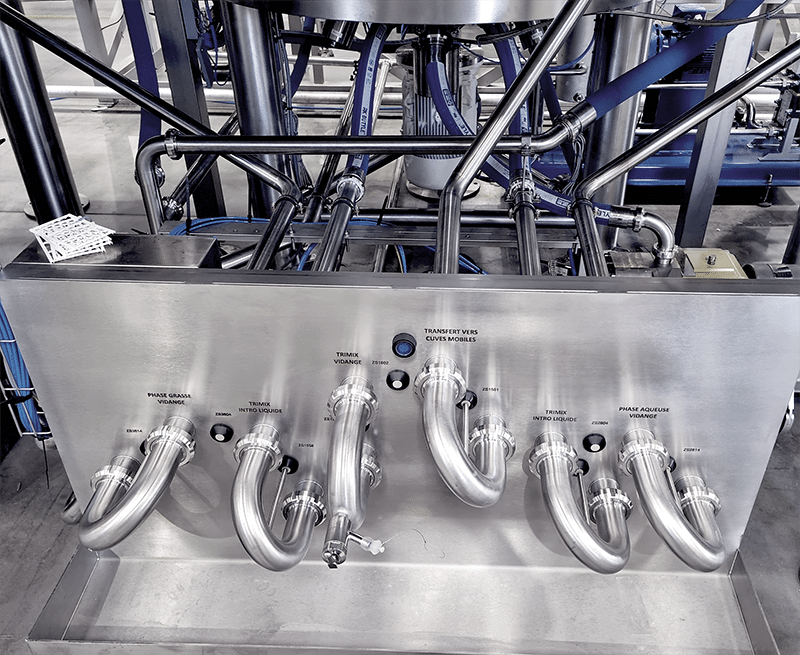
Las instalaciones de mezcla diseñadas por VMI integran el proceso global de fabricación. Desde la dosificación de la materia hasta el almacenamiento de los productos acabados, suministramos soluciones industriales llave en mano. Los ingredientes se almacenan o preparan en tanques de proceso y después se dosifican y transfieren a los tanques de fabricación. De acuerdo con su pliego de condiciones, un panel de distribución controla con precisión los flujos de productos.
La instalación global incluye tanques de proceso para los productos acabados: almacenamiento, mantenimiento o puesta a temperatura y puesta en suspensión. Entonces, se determina la agitación según la viscosidad, la densidad del producto y el proceso deseado.
Integración segura de nuestras instalaciones en sus entornos de producción
Nuestras unidades de mezcla están diseñadas de conformidad con las condiciones de fabricación en entorno controlado. Las salas blancas, también llamadas salas limpias, requieren especificaciones precisas en cuanto a los materiales, la temperatura, la calidad del aire, la higrometría, el mantenimiento, etc.
Nuestras plataformas de producción integradas en entorno estéril pueden instalarse conjuntamente con una sala gris para el almacenamiento (materias primas, detergentes, grupo de regulación térmica, tanques LIS, etc.) y los accesos de mantenimiento.
También le ayudamos en la clasificación en zonas de los lugares de riesgo y en la propuesta del equipo ATEX más adecuado para los riesgos de explosión identificados, de conformidad con la normativa.
Tecnologías de homogeneización: de la simple a la triple agitación
Desde hace más de 70 años, VMI diseña y fabrica una gama completa de agitadores para cubrir los procesos más variados: dilución, disolución, suspensión, homogeneización, dispersión o emulsión. Nuestros mezcladores y homogeneizadores satisfacen tanto las necesidades convencionales que sólo requieren una agitación simple como las más complejas que necesitan una aplicación que combine varios efectos mecánicos y físicos.
La tecnología de triple agitación desarrollada por VMI garantiza una homogeneización óptima por circuitos de circulación internos gracias a los 3 movimientos coaxiales independientes:
- Una agitación fondo de tanque con un emulsor-homogeneizador que garantiza una perfecta dispersión de los polvos y una finura de emulsión (rotor-estátor)
- Una agitación periférica co-rotativa o contra-rotativa para la homogeneización y, llegado el caso, la transferencia térmica (paleta ancla y raspadores)
- Una agitación central de flujo axial para la homogeneización y la circulación (tripalas anchas)
Fabricación al vacío
Sistemas de introducción de materias primas
Muchos procesos de fabricación de productos químicos, cosméticos, farmacéuticos o alimentarios ponen en práctica la dispersión de materias sólidas en forma de polvos en fases líquidas o pastosas. El éxito de esta fase crítica de homogeneización depende de la capacidad del equipo para gestionar dos regímenes hidrodinámicos distintos y garantizar simultáneamente la dispersión de partículas y la mezcla de fases líquidas.
Introducción al vacío de polvos en el centro del emulsor
VMI ha diseñado y patentado un rotor-estátor para permitir una recirculación interna en el tanque en dos fases: crear una depresión adicional que facilite la introducción y humectación de los polvos y, después, continuar una homogeneización fina de polvos y líquidos.
Este diseño permite dispersar eficazmente las partículas en una mezcla con un alto caudal y evita los inconvenientes de la recirculación externa al reducir las pérdidas de producto y limitar las zonas de retención. De este modo, los polvos se introducen directamente en el centro de la zona de mezcla, eliminando los riesgos de aglomeración de las partículas y de proyección de los polvos a través de la fase líquida. De esta forma se mejora la capacidad de producción y se facilita la limpieza gracias a la ausencia de tuberías de recirculación.
Las ventajas de la producción en atmósfera controlada
Además de la introducción de materias primas, la mezcla en atmósfera controlada presenta las siguientes ventajas:
- Mejora de la finura de la emulsión y, por tanto, de la textura del producto final gracias a la mezcla al vacío
- Reproducibilidad de la producción de un lote a otro, con una calidad constante de la mezcla
- Ahorro del tiempo de producción al permitir eliminar las burbujas de la mezcla directamente en el tanque de fabricación
- Utilización de la presurización para ayudar al vaciado del tanque al final de la producción
La regulación térmica por circuito de agua a presión: una solución económica y eficaz
Los tanques de fabricación tienen una doble camisa para el calentamiento y el enfriamiento del producto. Esta doble camisa desempeña dos funciones: garantizar el aumento de la temperatura del producto para permitir la emulsión de las fases grasas y acuosas y, al final del proceso, enfriar el producto acabado para el envasado o el almacenamiento intermedio.
VMI ha desarrollado un sistema de regulación térmica por circuito de agua a presión, que tiene muchas ventajas respecto a la regulación por inyección directa de vapor y agua fría. El grupo de regulación está compuesto por dos intercambiadores distintos (vapor/agua fría) y una bomba de recirculación en la doble camisa del tanque.
- Ausencia de choques térmicos: las diferencias de temperatura entre caliente y frío son limitadas, el aumento de temperatura de la doble camisa es progresivo y óptimo. Se conservan las propiedades y la calidad del producto.
- Reducción de los consumos: el agua no se pierde, circula por el intercambiador y vuelve al grupo de frío. Esto supone un ahorro de energía en comparación con la regulación por inyección directa, ya que las aguas perdidas deben enfriarse antes de ser expulsadas. La regulación térmica por circuito de agua es una opción para reducir su huella ambiental. Todos nuestros grupos de regulación están equipados con un purgador de flotador que permite recuperar los condensados para realimentar su caldera de vapor.
- Ahorro de tiempo: no se pierde tiempo entre dos ciclos térmicos, el calentamiento comienza inmediatamente después de una fase de enfriamiento o a la inversa.
Limpieza y Esterilización In Situ (LIS/EIS)
Las normativas de higiene cada vez más exigentes tienen por objeto garantizar la seguridad y la salud de los consumidores. La limpieza, la desinfección e incluso la esterilización de los equipos de producción garantizan la seguridad de los procesos de producción.
VMI diseña sistemas de Limpieza In Situ (LIS) y Esterilización In Situ (EIS) eficientes, integrados y automatizados.
Una limpieza eficaz es una combinación de varios factores:
- Un conjunto de elementos mecánicos (boquillas de lavado) dentro del tanque de producción
- Temperaturas de agua adaptadas. Se instalan tanques específicos en la zona gris donde las aguas de lavado se almacenan, se calientan y/o enfrían con glicol y vapor de agua.
- Una dosificación automática de detergentes y desinfectantes, según la acidez o la alcalinidad de los ingredientes
- Una sucesión de ciclos a adaptar según el producto fabricado: prelavado, remojo, lavado en recirculación, aclarado en recirculación, aclarado en agua perdida y empuje por aire para evacuar el agua y secar el equipo.
- Nuestro sistema LIS realizar un último ciclo: la esterilización, mediante la inyección de vapor de agua.
La IHM permite programar y controlar los ciclos de limpieza, así como crear recetas estándar de limpieza según el tipo de producto acabado.
Los múltiples beneficios de un sistema LIS
- Calidad de limpieza
- Ausencia de zonas muertas en el tanque
- Ausencia de zonas de retención en las tuberías -circuito de circulación interna- y control de la velocidad del fluido
- Calidad de producción
- Evita las no conformidades
- Elimina los riesgos de contaminaciones cruzadas o microbianas
- Repetibilidad de los procesos
- Automatización del proceso de limpieza a través de la IHM
- Test de aceptación: registro y encadenamiento automático de los ciclos de lavado
- Desarrollo sostenible y ahorro
- El consumo de agua se divide por tres o cuatro en comparación con un lavado manual
- Control y optimización de las cantidades de detergente utilizados
- Reducción de los tiempos de no producción, que son los tiempos de lavado
- Seguridad
- Implementación segura, con poca o ninguna intervención humana
- Control de la calidad de limpieza al final de LIS: ausencia de detergente antes del lanzamiento de una nueva producción
Cualificación de los equipos para garantizar la seguridad de las instalaciones
Las tecnologías de mezcla de VMI se desarrollan de conformidad con las normas y reglamentos del sector farmacéutico y cosmético.
A lo largo de todo el diseño a medida del equipo, validamos las etapas fundamentales para la integración del equipo en su entorno y para su correcto funcionamiento a largo plazo: validación del PID, análisis funcional, respeto de las GMF, análisis y gestión de los riesgos, normas 21 CFR parte 11, GAMP5, etc.
Todas las fases y controles se realizan con una atención constante para preparar las pruebas y las documentaciones completas para la cualificación de la instalación (CI) y la cualificación operativa (CO).
Las instalaciones industriales se ensamblan completamente y se prueban en nuestros talleres para realizar las pruebas de aceptación: FAT – Factory Acceptance Test. El cliente puede asistir y participar en el FAT de forma presencial o a distancia.
A continuación, el equipo se desmonta y se envía, y después nuestros equipos lo vuelven a ensamblar en el centro de fabricación. Se realiza otra serie de pruebas para validar la configuración final del equipo: SAT – Site Acceptance Test.